Process Excellence [1.9]
CRM Cyprus Ltd via specialized Consultants undertakes the institution and implementation of a Process Excellence System adapted to each and every Company’s needs.
The permanent business objective should be excellence even in a competitive environment where the prevailing conditions seem to impose discounts in quality and shortcuts in the efforts of its assurance.
Even if perfection itself is a utopia, its approach is a road through a set of procedures and guidelines that, when implemented through each and every part of the constituent production or service elements, can achieve excellent results even with the existing business data. The maximization of the business performance is achieved via the institution of a Process Excellence philosophy.
The implementation of this philosophy showed that roughly 60% of the actions performed during operations could be deleted without any consequences for the business objectives.
The philosophy approach of “Process Excellence” contributes in profit growth targeting a corresponding reduction in waste of time, floor space and expenses as well as additional 8 “common sins” of operations.
Implementation is realized via three pillars:
- Lean [1.9.1]
- 6 Sigma [1.9.2]
- Design Excellence [1.9.3]
These Pillars are briefly analysed below.
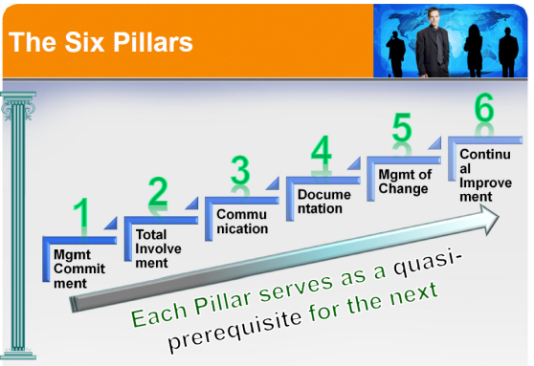
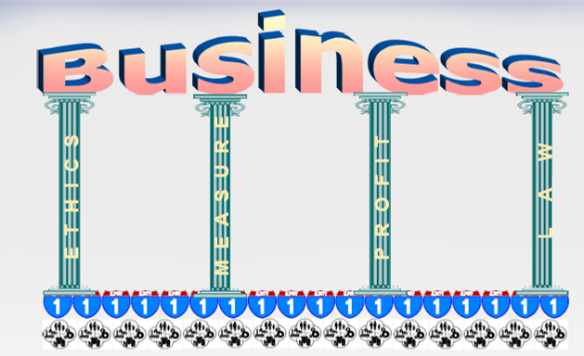
Lean [1.9.1]
Lean
The process that is free of:
- Redundant steps in order to minimize working time and production of any business output (physical product, service)
- Surplus stock in the intermediate process phases that occupy vital space
- Excess personnel that could be used elsewhere more productively
- Overspending time on peripheral support systems so as for them to function for less time while at the same time achieving energy saving thus more environmentally friendly management
Lean tools comprise:
- Lean Μanufacturing
- 5S
- Single-Minute Exchange of Die (SMED)
- Visual Factory
- Value Stream Mapping – VSM
- Mistake Proofing (Poka Yoke)
- Lean Flow
- Root Cause Analysis – RCA
- Scheduling
- Kaizen
- Jidoka
6Σ (6 Sigma) [1.9.2]
6Σ (6 Sigma)
The Pillar that, through its tools and systematic approach, is used to further improve an existing process/ procedure to avoid waste by minimizing substandard physical products or services that damage the Company’s image.
The steps followed by 6 Sigma are:
- Define
- Control
- Measure
- Analyze I
- Improve – Innovate
- Analyze II
Design Excellence [1.9.3]
Design Excellence
The specific pillar is the only solution-tool of designing processes-procedures in order for them to be the best prior to their implementation. The application of this pillar’s principles filters any deviations in product or service output at a preventive level i.e. prior to introducing them in the production process.
The steps followed by Design Excellence are:
- Define
- Measure
- Analyze
- Design
- Validate-Verify
- Control
Lean [1.9.1]
Lean
The process that is free of:
- Redundant steps in order to minimize working time and production of any business output (physical product, service)
- Surplus stock in the intermediate process phases that occupy vital space
- Excess personnel that could be used elsewhere more productively
- Overspending time on peripheral support systems so as for them to function for less time while at the same time achieving energy saving thus more environmentally friendly management
Lean tools comprise:
- Lean Μanufacturing
- 5S
- Single-Minute Exchange of Die (SMED)
- Visual Factory
- Value Stream Mapping – VSM
- Mistake Proofing (Poka Yoke)
- Lean Flow
- Root Cause Analysis – RCA
- Scheduling
- Kaizen
- Jidoka
6Σ (6 Sigma) [1.9.2]
6Σ (6 Sigma)
The Pillar that, through its tools and systematic approach, is used to further improve an existing process/ procedure to avoid waste by minimizing substandard physical products or services that damage the Company’s image.
The steps followed by 6 Sigma are:
- Define
- Control
- Measure
- Analyze I
- Improve – Innovate
- Analyze II
Design Excellence [1.9.3]
Design Excellence
The specific pillar is the only solution-tool of designing processes-procedures in order for them to be the best prior to their implementation. The application of this pillar’s principles filters any deviations in product or service output at a preventive level i.e. prior to introducing them in the production process.
The steps followed by Design Excellence are:
- Define
- Measure
- Analyze
- Design
- Validate-Verify
- Control